3D Scanning and Printing
We learned this week about 3D printing, about their types, about 3D scanning , and we made samples of our design and printed them on the printer. It was a great experience and presented It was documented in this assignment.
This week's mission
individual assignment:
design and 3D print an object (small, few cm3, limited by printer time)that could not be made subtractively
3D scan an object (and optionally print it)
group assignment:you can click here
- test the design rules for your 3D printer(s)
1. What is 3D printing?
3D printing is the automated process of building a three-dimensional object by adding material rather than taking material away (as in drilling or machining). The process, also known as additive manufacturing, was first introduced in the late 1980s. It was first commercially used as a rapid prototyping method in the aerospace and automotive industries.
2. How does 3D printing work?
To create a 3D printed object, you use an “additive process”. The three-dimensional object is created by laying down successive layers of material until the object is finished.
3. Which types of 3D printing technologies are there?
3D printers use one of the following methods to build an object layer by layer:
3D PRINTING TECHNOLOGY 1: FUSED DEPOSITION MODELING (FDM)
This is the most common technology used in desktop 3D printers. Thermoplastic material is heated and extruded through a nozzle. The nozzle deposits the molten material layer by layer onto a build platform. Each layer sticks to the one beneath it.
3D PRINTING TECHNOLOGY 2: STEREOLITHOGRAPHY (SLA)
The build platform is lowered into a bath filled with a special liquid photopolymer resin. The resin is light-sensitive and becomes solid when exposed to a laser beam. Each cross section of the 3D model is traced onto the layer of cured resin that came before it. This is repeated layer by layer until the 3D object is completed.
In FDM the object is built from the bottom up, in SLA it’s the other way round.
3D PRINTING TECHNOLOGY 3: SELECTIVE LASER SINTERING (SLS)
This process involves a laser beam fusing powdered material together. The first layer of powdered material is evenly rolled onto the build platform after which the layer of the 3D model is fused together by a laser. Next, the build platform is lowered by the width of one layer, and the next layer of powder is rolled into position. This process is repeated until the 3D object is finished. Since the object is surrounded by (unused) material throughout the duration of the build, support structures are not necessary like they
sometimes are with the FDM process.
Many different materials can be used with this technology from plastics to metals.
3D PRINTING TECHNOLOGY 4: SELECTIVE LASER MELTING (SLM)
SLS works on the same principal as the SLS process but uses a higher intensity laser and only metal powder. In this process, the tiny metal particles are actually melted together to form a solid piece of metal as if machined from one solid block.
3D PRINTING TECHNOLOGY 5: BINDER JETTING
Binder Jetting also uses a powder bed as its source of material. But instead of a laser, the powder, e.g. metal, is first “glued” together using an adhesive binder after which the object is heat-treated in a kiln to set or fuse the material.
ultimaker 3d printer I used
Features summary
Designed by experts and enriched by our global community, Ultimaker 2+ and Ultimaker 2 Extended+ perform even complex 3D printing
tasks with ease. They excel at printing bridging, overhangs, and accurate details.
- Build volume: up to 223 x 223 x 305 mm (8.8 x 8.8 x 12 inches)
- Up to 20 micron (0.001 inch) layer resolution
- Print head travel speed: 300 mm/s
- Open filament system – print with any 2.85 mm material
What are 3D printing filaments? What do I need them for?
The word “filament” comes from the Latin word for “thread” which is “filum”. It is used to describe anything that is thread-like in structure.
In 3D printing, filament is the name given to the material used by the 3D printer to print. In printers using FDM technology, the material comes in the form of a filament coiled around a small spool. The filament is then fed into the extruder through a guide tube. Usually, thermoplastics for 3D printers using the FDM method come in the shape of filaments.
Some 3D printers, mostly industrial ones, use material pellets instead of filaments. This brings down the cost of 3D printing material significantly. Other 3D printers, the SLA printer types, use liquid resin instead of strands of thermoplastics.
What types of 3D printing filaments are there?
There are many different kinds of 3D printing filaments. First of all, they come in two conventional diameters: 1.75mm and 3.00mm.
The most common materials used in FDM 3D printing are PLA and ABS. They are popular for their ease of use (ABS being a little more complicated to 3D print), and their affordability.
But as far as what materials you can print with are concerned, there are almost no limits. It is possible to print in pure metal, food and all sorts of thermoplastics whereby metal and food don’t come in filament form for obvious reasons. But don’t be confused, if you see a spool of filament that says metal on it. In this case, metal dust is mixed with thermoplastic material for use in desktop FDM 3D printers.
Here is a comprehensive article on the many types of
3D printer filament.
Before starting the printing process
we need a design and you can bring it ready from one of the websites for 3D models or design it as I did.
I have designed a mobile stand using Fusion 360
First we draw a vertical line and then follow it with a horizontal line
Then we follow them with a sharp angle line as shown in the picture
We apply a command fillet to get rid of the sharp corner then comment offset
Then draw a square as a base for a stand and apply a Fillet command and then an offset command
Right-click on the drawing,Then he chose press pull
After preparing the design, we save it in STL format and transfer it to Ultimaker2+ Cura software
- To move the print pattern into position in the print area
- for change Model size
- Rotate the model and find the best printing base
- To reverse the model around its axis
- When printing more than one model at a time, each of them can be equipped with their own settings
- To open the file, obj or stl
Stand after printing
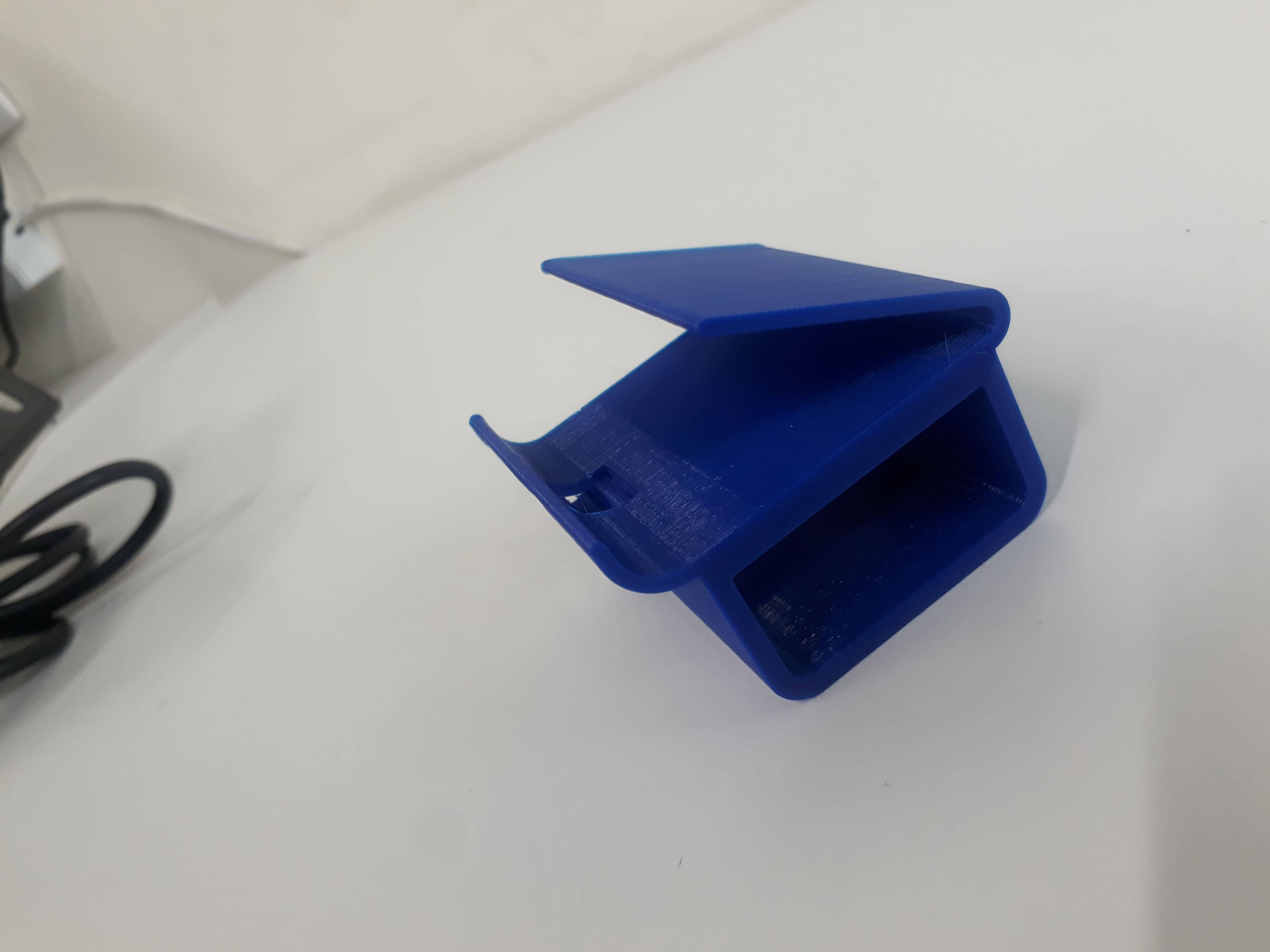
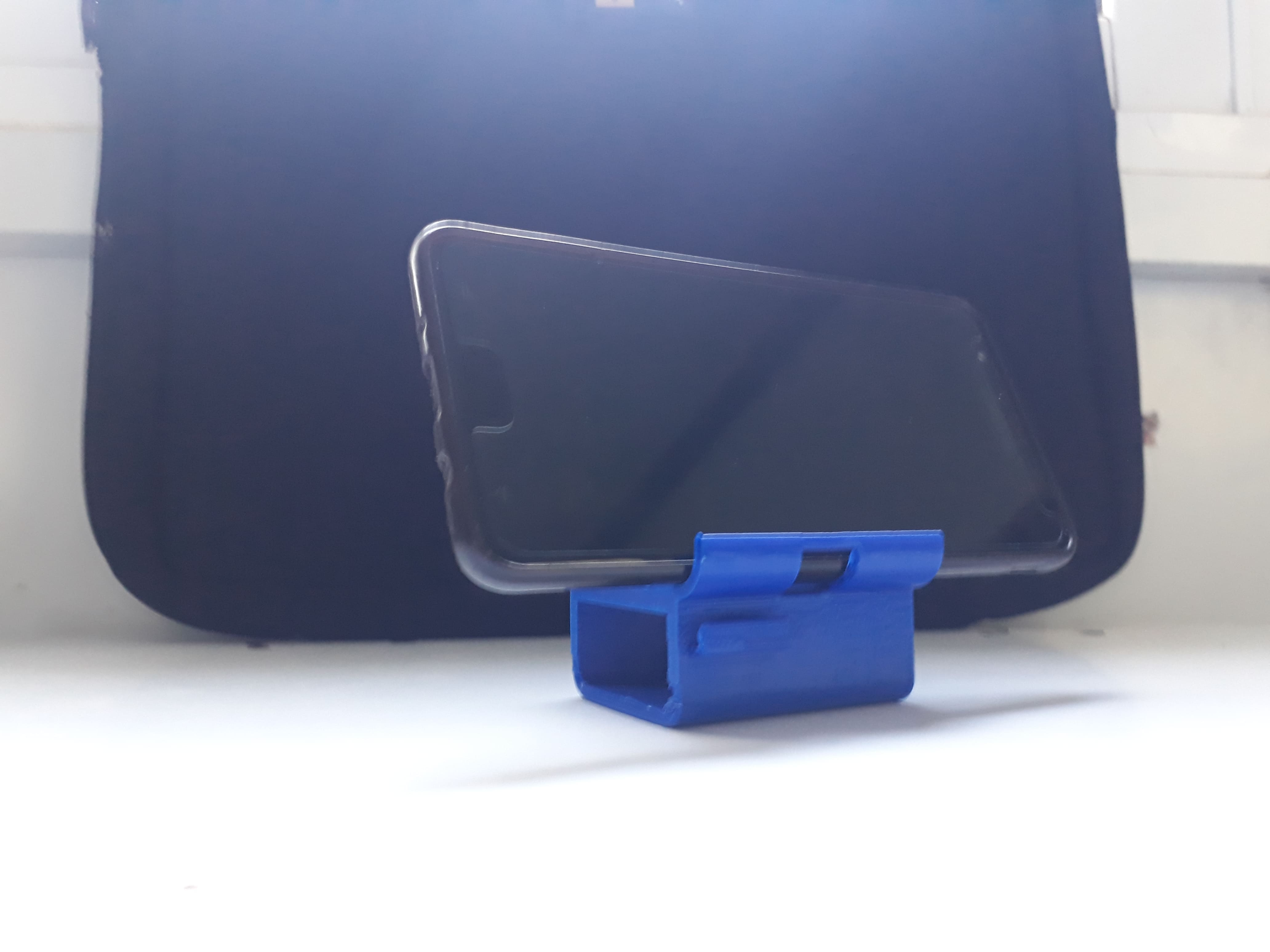
3D scanning
3D scanning is the process of analyzing a real-world object or environment to collect data on its shape and possibly its appearance (e.g. colour). The collected data can then be used to construct digital 3D models.
A 3D scanner can be based on many different technologies, each with its own limitations, advantages and costs. Many limitations in the kind of objects that can be digitised are still present. for example, optical technology may encounter many difficulties with shiny, reflective or transparent objects.
Functionality
The purpose of a 3D scanner is usually to create a 3D model. This 3D model consists of a point cloud of geometric samples on the surface of the subject. These points can then be used to extrapolate the shape of the subject (a process called reconstruction). If colour information is collected at each point, then the colours on the surface of the subject can also be determined.
3D scanners share several traits with cameras. Like most cameras, they have a cone-like field of view, and like cameras, they can only collect information about surfaces that are not obscured. While a camera collects colour information about surfaces within its field of view, a 3D scanner collects distance information about surfaces within its field of view. The "picture" produced by a 3D scanner describes the distance to a surface at each point in the picture. This allows the three dimensional position of each point in the picture to be identified.